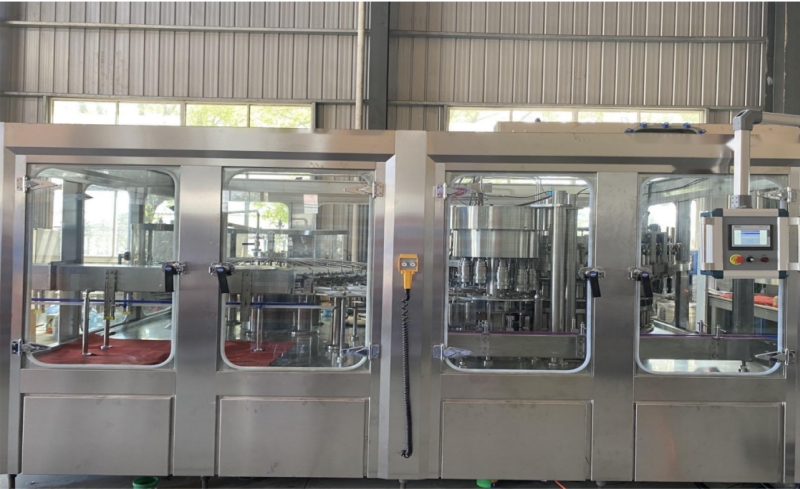
Up to 28,000 bottles per hour
filling heads
Up to 50 filling heads
beverage types
Ideal for soda, cola, and carbonated soft drinks
Overview of Carbonated Beverage Filling Machine
If you want to improve the filling efficiency of carbonated beverages, HuiRun’s high-efficiency carbonated beverage filling machine is your best choice. Our equipment specially designed for carbonated beverage filling can significantly optimize your carbonated beverage production line, bringing a higher level of automation and production stability. Whether it’s soda water, beer or sparkling juice, this system can be efficiently adapted to meet diverse demands.
This carbonated beverage filling machine adopts constant pressure filling technology, precisely controlling the ratio of gas to liquid, reducing foam generation and filling errors, and ensuring stable product quality. The entire line design focuses on energy conservation and consumption reduction, making it an ideal component of modern carbonated beverage production lines. The HuiRun system also supports the filling of niche carbonated beverages such as kombucha, bringing greater flexibility to your product portfolio.
By choosing HuiRun carbonated beverage filling machines, you are not only upgrading your equipment but also building an efficient and reliable production system. Learn how we can help your carbonated beverage production line enhance its competitiveness and achieve sustainable growth.
features of carbonated beverage filling machine
carbonated soft drinks(CSD) filling machine is particularly suitable for filling and sealing plastic bottles in the beer and Coke, Sprite, soda water, speech water, cocktails, flavored water.. carbonated beverage industry, and can perform secondary exhaust on the bottle body in the filling valve. It can ensure that the oxygen increase of beer is minimized during the filling process.
The filling machine is equipped with 12 to 50 valves, with a production speed of 3,000 to 28,000 bottles/hour and a capacity from 200 ml to 1 liter.
It uses high-precision pneumatic electric filling valves, or mechanical filling valves with double pre-vacuuming, and uses carbon dioxide or nitrogen as counter-pressure gas, without bottles, pre-vacuuming, or filling.
The filling and capping are designed as a whole, using the principle of equal pressure filling. The bottles enter the filling machine through the bottle feeding star wheel, reach the predetermined center of the star wheel, and then the filling valve descends along the supporting cam to center the cans and pre press and seal them.
The sealing pressure is generated by one cylinder in addition to the weight of the centering cover itself. The air pressure inside the cylinder can be adjusted by the pressure reducing valve on the control board according to the material of the can, with a pressure of 0-40KP (0-0.04MPa), At the same time, by opening the pre inflation and back pressure valves, while opening the low-pressure annular channel, the back pressure gas in the filling cylinder rushes into the bottle and flows into the low-pressure annular channel. This process is used to implement a CO2 flushing program to remove air from the bottle, and through this program, the amount of oxygen added during the filling process is relatively minimized.
After the pre charge valve is closed, an equal pressure is established between the bottle and the cylinder. The liquid valve is opened by a spring under the action of the operating valve stem, and filling begins. Through three inlet tanks, the material flows down the bottle wall, and the pre charge gas in the bottle returns to the filling cylinder through the air valve.
When the liquid level of the material reaches the return pipe, the return gas is blocked, filling stops, and an overpressure is generated in the upper gas part of the bottle to prevent the material from continuing to flow down.
Pull the fork to close the gas and liquid valves, and through the exhaust valve, the pressure in the bottle is balanced with atmospheric pressure. The exhaust channel is kept away from the liquid surface to prevent liquid from being carried out during exhaust.
During the exhaust period, the gas at the top of the bottle expands, and the material in the return pipe falls back into the bottle, emptying the return pipe.
At the moment of bottle discharge, the centering cover is lifted by the action of the cam, and under the action of the inner and outer protective plates, the bottle leaves the star wheel and enters the capping machine.
The main electrical components of this machine adopt high-quality configurations such as Siemens PLC and Sike proximity switches. The company’s senior electrical engineers have designed a reasonable configuration form, and the entire production speed can be set on the touch screen according to requirements. All common faults will automatically alarm and provide corresponding fault cause locations. Based on the severity of the fault, the PLC will automatically determine whether the host can continue to run or stop.
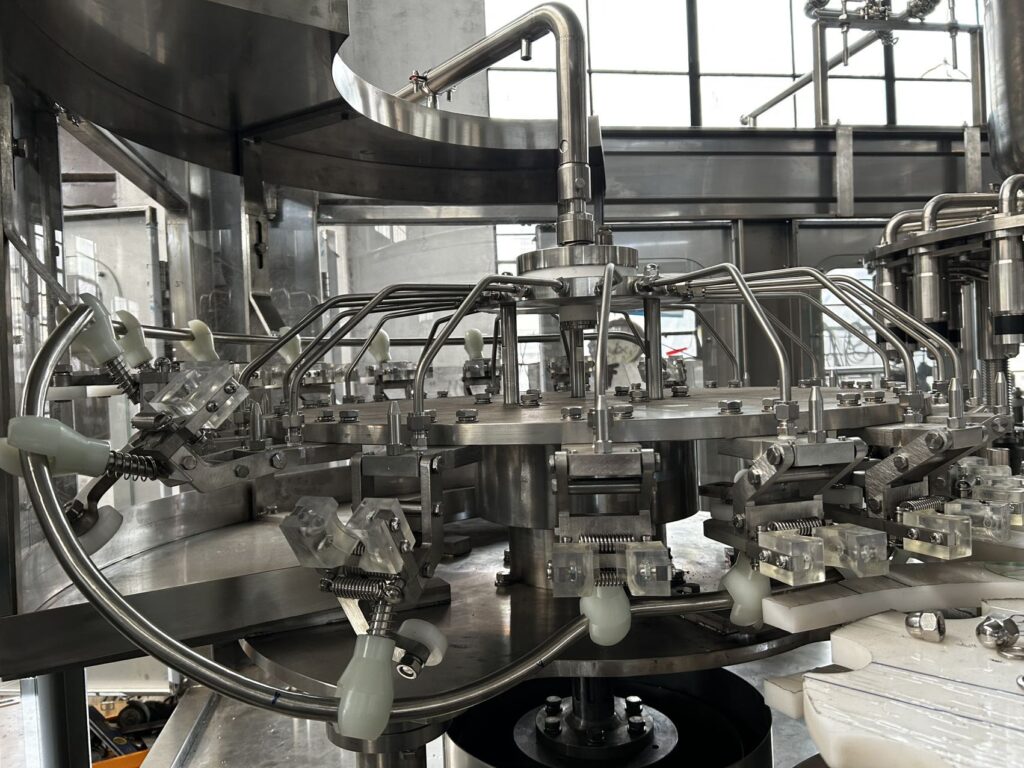
Executing Efficient Rinsing in Carbonated Beverage Filling Machines
Before the carbonated soft drink filling line begins its main operation, the rinsing system of the carbonated drinks filling machine thoroughly cleans containers. This crucial step in soft drink bottling lines uses water or media supplied by the customer. The beverage bottling machine’s rinsing process eliminates impurities, ensuring containers are pristine before being filled with carbonated drinks.
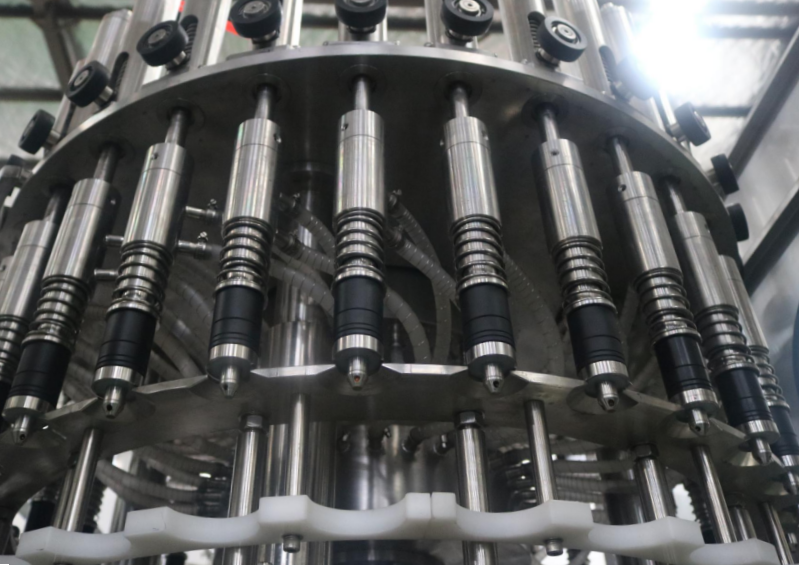
Filling with Care: The Heart of Carbonated Beverage Filling Machines
The filling system of the carbonated drinks filling machine is specifically engineered for carbonated beverages. This advanced soft drink bottling line efficiently fills bottles while minimizing bubbles and preventing carbon dioxide leakage. The carbonated soft drink filling line maintains optimal carbonation levels throughout the process, ensuring the quality of the final product.
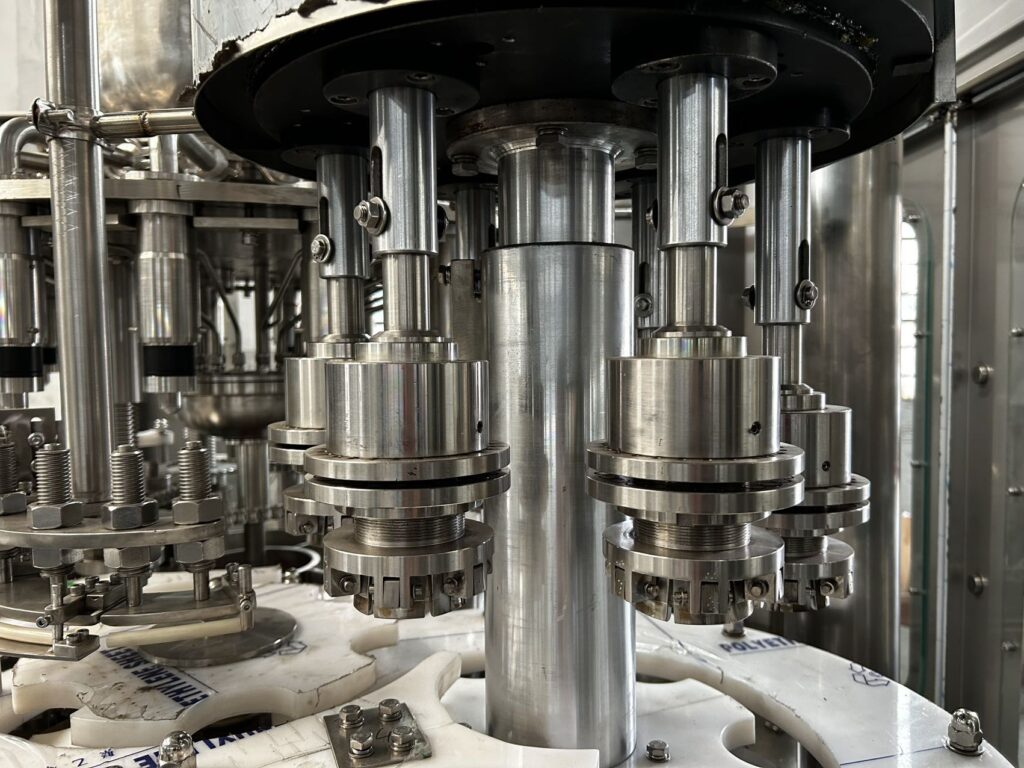
Precision Capping in Carbonated Beverage Filling Machines
After the filling process, the capping system of the carbonated drinks filling machine securely seals the containers. This critical component of the carbonated water filling machine ensures no leaks, maintaining carbonation and prolonging shelf life. The beverage bottling machine’s capping system plays a vital role in preserving product quality, making it an essential part of soft drink bottling lines.
Technical advantages of carbonated beverage filling machine
1. Advanced control system: The glass bottle filling machine adopts PLC, frequency converter, and human-machine interface control system. It has excellent control technologies such as frequency conversion speed regulation, automatic bottle filling, and no filling without cans. Through various sensors on the equipment, the production speed and quantity can be accurately displayed on the touch screen, and the production speed can be set on the touch screen according to user requirements.
2. Perfect protection mechanism: This filling machine has various protections for the main motor and other electrical appliances, such as overload, overvoltage, etc. At the same time, the touch screen will automatically display the corresponding various faults, which is convenient for users to find the cause of the fault.
3. High-quality electrical components: The main electrical components of this filling machine are all internationally renowned brands, and can also be customized according to customer requirements.
4. Intelligent operation: The whole machine adopts PLC computer program interface touch screen buttons, with automatic control of liquid level in the material cylinder, bottleless filling, bottleless capping and other functions, using frequency converter stepless speed regulation, digital display of production capacity, and extremely convenient adjustment.